Non woven Manufacturing
Every step of our manufacturing process is meticulously designed to ensure the highest quality and innovation in non woven fabrics. Here’s a detailed breakdown of our manufacturing journey:

WEB FORMATION
The journey of non woven fabric production begins with the crucial step of web formation. The characteristics of the fibrous web play a pivotal role in defining the final product’s physical properties. Various methods are employed for web formation, determined by the length of the fibers used. For staple-length fibers, methods akin to textile carding are utilized, while short fibers find their way into a wet-laid process reminiscent of papermaking. Furthermore, the innovative spun-laid method involves creating a web directly from filaments emerging from an extruder. This initial stage lays the foundation for what follows.
WEB BONDING
Fibrous webs possess minimal mechanical strength, necessitating additional manufacturing processes to transform them into fabrics with practical properties. The bonding of these webs is the next critical step.
One such method is “needle punching,” where barbed needles, arranged on a board, mechanically interlock the fibers by punching them into the web. Another technique, “stitch bonding,” consolidates fiber webs with knitting elements, often with the inclusion of yarn to interlock the fibers.
Thermal bonding, on the other hand, employs heat to stabilize a web made of thermoplastic fibers, eliminating the need for additional binders.
Chemical bonding involves the application of chemical binders, with latex being a common choice, while hydro entanglement uses fluid forces to lock fibers together, achieved through the careful use of water jets.
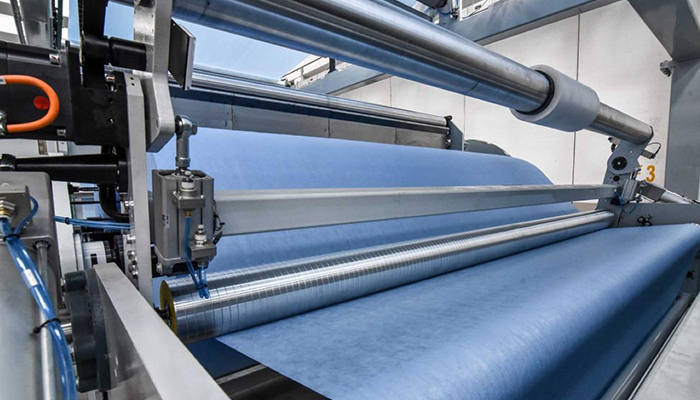
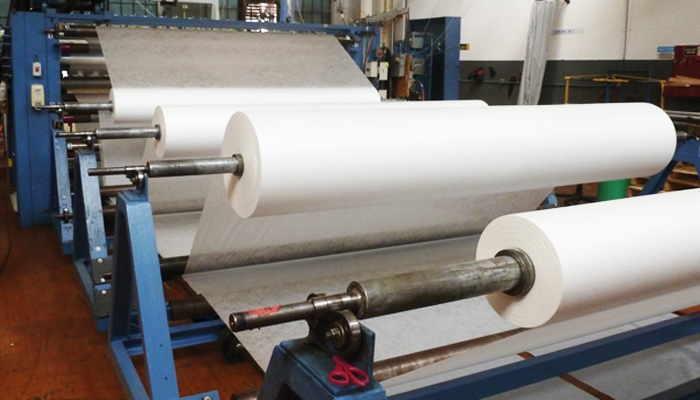
FINISHING & CONVERTING
The final chapters in the non woven manufacturing process involve finishing and converting. Finishing encompasses operations like coating, laminating, calendaring, and embossing to impart specific surface properties to the fabric. Treatments like corona and plasma treatments alter the fabric’s wetting properties, while wet chemical treatments can bestow anti-static, anti-microbial, flame-retardant, and other desired properties. Once the finishing touches are applied, the fabric is typically cut to the customer’s specified width and rewound, making it ready for shipment. This crucial step is known as converting.